Solution
- Standardized supplier selection process
- Standardized product category quality standards
- Supplier visit and on site mass production process improvement and audit
- 75 % reduced quality issues during manufacturing process based on LEAN good practices
- Improved manufacturing process saved 250.000 USD with each production batch
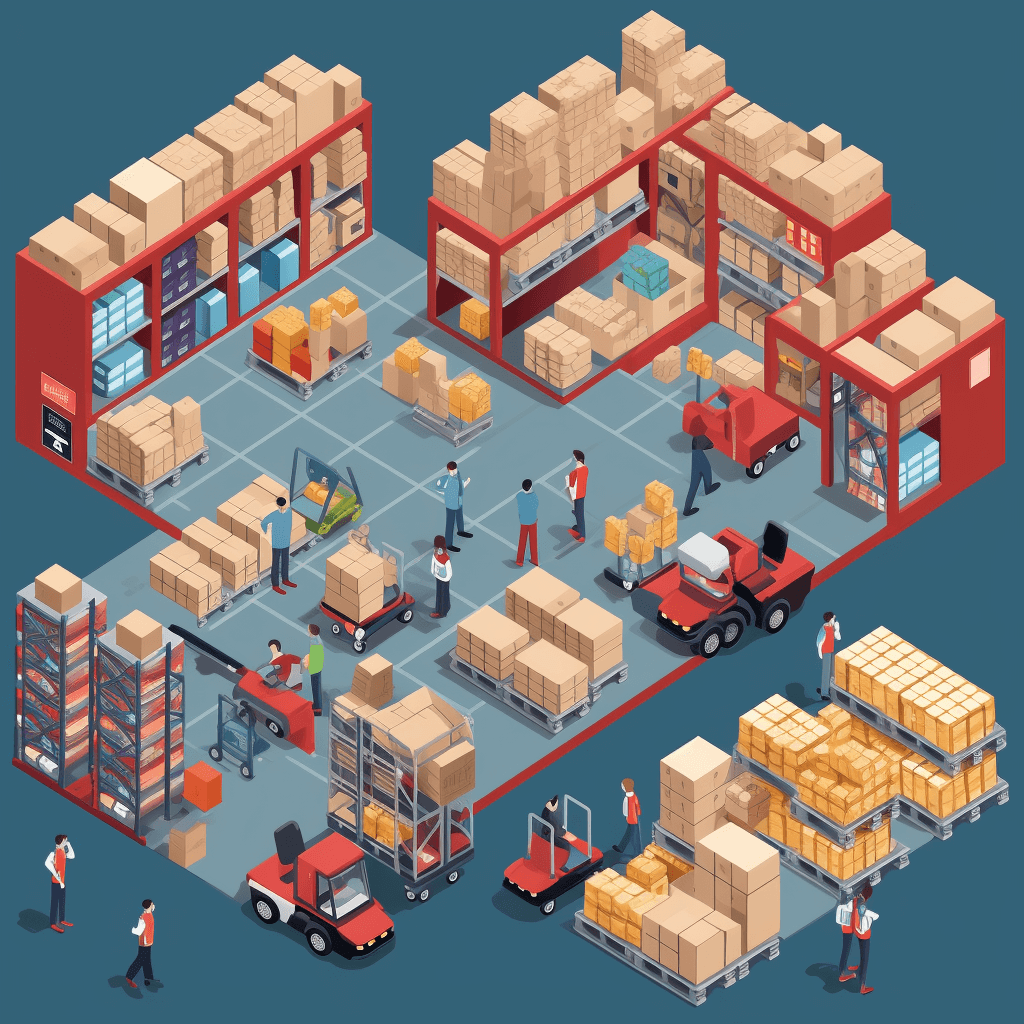
Identifying the Challenges
In the dynamic realm of project-based companies, winning tenders and delivering exceptional results are paramount. However, our client found themselves trapped in a cycle of inconsistency and quality issues. Their standard process involved receiving tender information, engaging with 3-4 suppliers, and ultimately opting for the cheapest option. Unfortunately, this often led to lengthy discussions and disputes over product quality upon delivery.
Collaborative Exploration and Focus
Our initial assessment revealed a lack of standardized supplier selection processes and a stagnation in introducing new suppliers. To address these challenges head-on, we collaborated closely with the company to identify key product groups that deserved focused attention. This strategic approach allowed us to introduce standardized quality standards within each category, fostering ongoing improvements through close collaboration with suppliers.
Going the Extra Mile for Quality
While the establishment of standardized quality standards was a significant leap forward, we understood that more steps were needed to tackle persistent claims. To achieve this, we implemented a standardized supplier evaluation system and conducted on-site visits during order production. These visits provided an opportunity for our procurement and quality experts to meticulously analyze the main quality defects and actively seek solutions to enhance overall product quality.
Implementing Change and Reaping Rewards
The implementation of these standardized processes, coupled with our proactive approach of visiting manufacturing plants in Asia, yielded remarkable results. By increasing the quality rate, the client managed to save a staggering $250,000 that would have otherwise gone to waste. This reduction in scrapped products not only translated into substantial cost savings but also bolstered the company's reputation for delivering much better quality to their clients.